Autores: Augusto Rodríguez, Francisco Barrios, Dasset Gallardo, Héctor Sanzana / Centro de Ingeniería Mecánica y Diseño Industrial (CIMECDI) – FIIDT.
Las siglas del PLC significan Controlador Lógico Programable; y se trata de un dispositivo digital o computadora empleada en la automatización industrial cuyo objetivo consiste en controlar las líneas de montaje en las fábricas mediante el control de las máquinas y sus respectivos procesos.[11]
Breve historia de los PLCs.
Desde el comienzo de la industrialización, el hombre ha buscado cómo hacer que los trabajos se realizasen de la forma más ágil y menos tediosa para el operador en cuestión. Los PLCs han sido un mecanismo clave en este proceso puesto que permiten, entre otras cosas, que ciertas tareas se realicen de forma más rápida y que el hombre evite su aparición en trabajos peligrosos tanto como para él [12], como para su entorno más próximo. De este modo, hoy en día estamos rodeados de estos mecanismos que, rebasando la frontera de lo industrial, pueden encontrarse en semáforos; gestión de iluminación en parques, jardines y escaparates; control de puertas automáticas; e incluso en el control de dispositivos del hogar como ventanas, toldos, climatización, etc.
El desarrollo de los PLCs fue dirigido originalmente por los requerimientos de los fabricantes de automóviles. Estos cambiaban constantemente los sistemas de control en sus líneas de producción de modo que necesitaban un modo más económico para realizarlo puesto que, en el pasado, esto requería un extenso re-alambrado de bancos de relevadores (procedimiento muy costoso). De este modo, a finales de los años 60, la industria necesitaba cada vez más un sistema de control económico, robusto, flexible y fácilmente modificable. Así, en 1968 aparecieron los primeros autómatas programables (APIs o PLCs). La compañía americana Bedford Associates sugirió así un Controlador Modular Digital (MODICON) para su utilización en una compañía de automoción y MODICON 084 fue el primer PLC con una aplicación industrial (1968). [12]
Los nuevos controladores debían ser fácilmente programables por ingenieros de planta o personal de mantenimiento, su tiempo de vida debía ser largo y los cambios de programa tenían que realizarse de forma sencilla. También se imponía que pudiera trabajar sin problemas en entornos adversos. Para ello se utilizó una técnica de programación familiar y se reemplazó el uso de relevadores mecánicos por otros de estado sólido. A principios de los 70, los PLC ya incorporaban el microprocesador. En 1973 aparecieron los PLCs con la capacidad de comunicación – Modbus de MODICON. De este modo, los PLCs eran capaces de intercambiar información entre ellos y podían situarse lejos de los procesadores y los objetos que iban a controlar. Así se incorporaron también más prestaciones como manipulación de datos, cálculos matemáticos, elementos de comunicación hombre-máquina, etc. A mediados de los años 70 – apareció la tecnología PLC, basada en microprocesadores bit-slice (ej. AMD 2901/2903) [12].
Los principales productores de PLCs en esos tiempos se convirtieron en compañías como: Allen-Bradley, Siemens, Festo, Fanuc, Honeywell, Philips, Telemecanique, General Electric etc. Además, se realizaron mejoras como el aumento de su memoria; la posibilidad de tener entradas/salidas remotas tanto analógicas como numéricas, funciones de control de posicionamiento; aparición de lenguajes con mayor número de funciones y más potentes; y el aumento del desarrollo de las comunicaciones con periféricos y ordenadores. Durante este periodo, las tecnologías dominantes de estos dispositivos eran máquina de estados secuenciales y con CPUs basadas en el desplazamiento de bit. Los PLC más populares fueron los AMD 2901 y 20903 por parte de Modicon. Los microprocesadores convencionales aportaron la potencia necesaria para resolver de forma rápida y completa la lógica de los pequeños PLCs. Así, por cada modelo de microprocesador, existía un modelo de PLC basado en el mismo, aunque fue el 2903 uno de los más utilizados. Sin embargo, esta falta de estandarización generó una gran variedad de incompatibilidades en la comunicación debido a la existencia de un maremágnum de sistemas físicos y protocolos incompatibles entre sí.
Fue en los año 80 cuando se produjo un intento de estandarización de las comunicaciones con el protocolo MAP (Manufacturing Automotion Protocol) de General Motor’s. Se consiguió también reducir las dimensiones de los PLC y se pasó a programar con una programación simbólica a través de ordenadores personales en vez de los terminales clásicos de programación. De hecho, hoy en día, el PLC más pequeño es del tamaño de un simple relevador. Así, en la década de los 80 se mejoraron las prestaciones de los PLCs referidas a: velocidad de respuesta, reducción de las dimensiones, concentración del número de entradas/salidas en los respectivos módulos, desarrollo de módulos de control continuo, PID, servo controladores, control inteligente y fuzzy.
Los años 90 mostraron una reducción gradual en el número de protocolos nuevos y en la modernización de las capas físicas de los protocolos más populares que lograron sobrevivir a los años 80. El último estándar, IEC 1131-3, trata de unificar el sistema de programación de todos los PLC en un único estándar internacional. Hoy en día disponemos de PLCs que pueden ser programados en diagramas de bloques, listas de instrucciones o incluso texto estructurado al mismo tiempo. Sin embargo, los ordenadores comenzaron a reemplazar al PLC en algunas aplicaciones e incluso la compañía que introdujo el Modicon 084 ha cambiado su control en base a un ordenador. [12]
El PLC como unidad consta de un procesador para ejecutar la acción de control sobre los datos de campo proporcionados por los módulos de entrada y salida. En un dispositivo de programación, la lógica de control se desarrolla primero y luego se transfiere al PLC.
Entonces, ¿qué puede hacer un PLC?
- Puede realizar tareas de conmutación de relex.
- Puede realizar el conteo, el cálculo y la comparación de los valores de proceso analógicos.
- Ofrece flexibilidad para modificar la lógica de control, cuando sea necesario, en el menor tiempo posible.
- Responde a los cambios en los parámetros del proceso en fracciones de segundos.
- Mejora la fiabilidad del sistema de control global.
- Es rentable para controlar sistemas complejos.
- El diagnostico de averías se realiza de manera más simple y más rápida
- Se puede trabajar con la ayuda de la computadora HMI (interfaz hombre-máquina)
Los PLC son insustituibles en muchas aplicaciones industriales y proyectos de control.
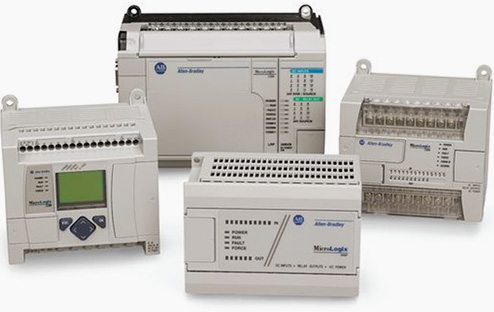
La gran ventaja de los PLCs a diferencia de las computadoras es la gran cantidad de entradas y salidas que pueden gestionar así como su durabilidad y capacidad de funcionamiento en entornos agresivos para la electrónica. Esto supone para las empresas un gran ahorro de dinero en mantenimiento. Pero los ahorros en mantenimiento no es únicamente el beneficio que aporta el PLC. También permite un aumento significativo de la vida útil de las máquinas industriales y sus equipos asociados. Sin duda las aplicaciones del PLCs en la industria moderna tienen un gran recorrido todavía.
El PLC ha supuesto una gran revolución en la automatización industrial. Estos aparatos electrónicos, debido a su facilidad de programación, han terminado por ser clave en la modernización de las empresas. Los autómatas programables han ido sustituyendo desde los años 60, los antiguos sistemas de control basados en circuitos eléctricos, relés, interruptores y otros componentes eléctricos.
Por otro lado, la evolución de los lenguajes de programación ha sufrido cambios importantes que han permitido desarrollar leguajes cada vez más sencillos, lo que supone un ahorro en tiempo de formación para los técnicos. Actualmente, los lenguajes de programación de autómatas se basan diagramas de contactos, programación basada en Basic o C o en lógica de estado.
Además, el PLC tiene un enorme campo de aplicación, como vamos a ver a continuación. En todos ellos se usa principalmente en maniobras de maquinaria. Aun así, también es útil para abarcar otros procesos y sistemas complejos de la industria moderna. En su uso industrial moderno es la conexión ainternet. Debido a este aspecto, que puede parecer sencillo a priori y no tan importante, permite una monitorización del funcionamiento desde cualquier ordenador en múltiples ubicaciones, tanto dentro de una fábrica como fuera de ella.
Aplicaciones del PLC en la industria moderna
Veamos ahora cómo los sistemas PLC se aplican en los diversos tipos de procesos industriales. De hecho, su utilidad abarca muchos flancos, desde aquellos de pequeña envergadura como dosificadores o montacargas, hasta complejos sistemas de control o líneas completas de producción. Solo hay que elegir el modelo adecuado para cada caso.
Conozcamos varios ejemplos ilustrativos.
Maniobras de maquinaria
Comenzamos con las maniobras de maquinaria. En este caso encontramos muchas aplicaciones interesantes:
- Máquinas de procesado de gravas, cementos y arenas.
- Máquinas industriales para la madera y los muebles.
- Maquinaria industrial del plástico.
- Máquinas – herramientas complejas.
- Máquinas de ensamblaje.
- Maquinaria de transferencia.
Maniobra de instalaciones
En el campo de la maniobra de instalaciones, también encontramos aplicaciones interesantes para el PLC:
- Instalaciones de seguridad.
- Instalaciones de calefacción y aire acondicionado.
- Instalaciones de plantas para el embotellado.
- Instalaciones de transporte y almacenaje.
- Instalaciones para tratamientos térmicos.
- Instalaciones de la industria de la automoción.
- Instalaciones industriales azucareras.
Industria automotriz
Hemos comentado la importancia de las aplicaciones de los PLC en la industria de la automoción. Y efectivamente, sus usos son muchos y muy variados e importantes:
- Aplicaciones en cadenas de montaje para soldaduras, cabinas de pintura, ensamblaje, etc.
- Uso en máquinas de herramientas como fresadoras, taladradoras, tornos, etc.
Fabricación de neumáticos
Muy emparentado con la industria automotriz, encontramos aplicaciones importantes para la fabricación de neumáticos:
- Control de maquinaria para la extrusión de gomas, el armado de cubiertas
- Control de sistemas de refrigeración, calderas, prensas de vulcanizado
Plantas petroquímicas y químicas
En el sector de la industria química también descubrimos una serie de usos importantes para el PLC:
- Aplicación en oleoductos, refinados, baños electrolíticos, tratamientos de aguas residuales y fecales, etc.
- Control de procesos como el pesaje, la dosificación, la mezcla, etc.
Otros sectores industriales
También observamos más aplicaciones en sectores diversos de la industria moderna:
- Metalurgia: control de hornos, fundiciones, laminado, grúas, forjas, soldadura, etc.
- Alimentación: empaquetado, envasado, almacenaje, llenado de botellas, embotellado, etc.
- Madereras y papeleras: serradoras, control de procesos, laminados, producción de conglomerados…
- Producción de energía: turbinas, transporte de combustibles, centrales eléctricas, energía solar.
- Tráfico: ferrocarriles, control y regulación del tráfico…
- Domótica: temperatura ambiente, sistemas anti robo, iluminación, etc.
La aplicación de PLC o autómatas programables cubren necesidades muy definidas. Así pues, ahora que se tiende a la automatización industrial total, estos instrumentos electrónicos aportan un número de ventajas enormes para la producción:
- Son ventajosos para una fábrica gracias a sus beneficios similares a la lógica cableada.
- Poseen una sencilla elaboración, por lo que no se pierde tiempo en los procesos en relación a otros instrumentos menos manejables.
- No requieren de modificación de instalaciones eléctricas y cableados. De hecho, las modificaciones se llevan a cabo en el mismo PLC.
- Se fabrican con el uso de muy poco material.
- Su coste es sensiblemente inferior a otros métodos más tradicionales.
- El mantenimiento es extremadamente económico en relación a otros sistemas, por lo que la producción apenas tiene que ser parada.
Finalmente podemos concluir que la importancia de los controladores lógicos programables es poder cumplir los requerimientos de productividad, eficiencia, precisión y fiabilidad que no era capaz de cumplir el antiguo sistema basado en relés. Hoy en día este tipo de sistema está presente no solo en los complejos programas industriales sino en la automatización de nuestras casas (sistema de luces, domótica, etc.)
Bibliografía
- Programmable controllers: an engineer’s guide, E.A.Parr, third Edition, 2003
- Controladores lógicos, Manuel Álvarez Pulido, Ed. Marcombo, 2004
- Programmable logic controllers: the complete guide to the technology, Clarence T. Jones,1996
- STEP 7 una manera fácil de programar el PLC de Siemens, Pilar Mengual, Ed. Alfaomega, 2010
- Controladores Lógicos Programables. FESTO Didactic. 2009
- Principios de Electrónica. Malvino, Edit Mc Graw Hill. 2012
- Instrumentación Electrónica. Sagat, Edit Prentice Hall. 2009
- Electrónica Industrial. T. Malloney, Edit Prentice Hall.2008
- Automatización y Control. Dorenates, Edit Mc Graw Hill, 2009
- https://core.ac.uk/reader/76583190
- La Importancia de los PLC’s en la industria de la electrónica https://www.logicbus.com.mx/importancia-del-plc.php
- PLC, Sistemas Lógicos Programables http://sistemaslogicosprogramablespsm.blogspot.com/
Contacto: orlandoaco2@gmail.com