Edgar Pérez, José Antonio País, José Padilla, Misael Coste. Centro de Ingeniería Mecánica y Diseño Industrial (CIMECDI). FIIIDT.
PROCESO DE SOLDADURA
- Comenzando a soldar
Antes de iniciar el arco eléctrico, Ud. debe conocer que sucederá en la punta del electrodo. Se generará una temperatura en el orden de los 3.300 y 5.550 °C entre el electrodo y la pieza a soldar. El “flux” o fundente del revestimiento se calentará transformándose en sales fundidas y en vapor. Estas protegerán al metal fundido de la acción de la atmósfera. De allí el nombre de SMAW proveniente de las siglas en inglés, ya explicado en el artículo anterior “Soldadura por Arco de Metal Protegido (Parte I)”.
El gas de protección generado evita la acción de los gases de la atmósfera sobre la soldadura, los que habitualmente causarían incorporación de hidrógeno y porosidad entre otros defectos. Una vez que el metal fundido se solidificó, la escoria también lo hará formando una cascarilla por encima de la soldadura. Esta se podrá retirar con la ayuda de un pequeño martillo con sus terminaciones en punta llamado piqueta. Se deberá tener muy en cuenta lo siguiente. Donde se apunte o apoye la varilla de soldadura es donde irá el metal fundido. El calor junto con el metal fundido saldrá del electrodo dirigido hacia la pieza en forma de “spray”. Por ello, el electrodo se deberá dirigir donde se desea aportar metal, manteniendo a su vez el arco.
La soldadura con arco protegido (SMAW) es un tipo de soldadura de uso muy común. Si bien no resulta difícil de ejecutar, requiere de mucha paciencia y práctica para poder adquirir la pericia necesaria. En una gran parte, los resultados obtenidos dependerán de la habilidad del soldador para controlar y llevar a cabo el proceso de soldadura. La calidad de una soldadura, además, dependerá de los conocimientos que este posea. La pericia solo se obtiene con la práctica. Hay seis factores importantes a tener en cuenta. Los dos primeros están relacionados con la posición y la protección del operario, y los cuatro restantes con el proceso de soldadura en sí.
Los mismos están detallados a continuación, a saber:
- Posición correcta para ejecutar la soldadura.
- Protección facial (se debe usar máscara o casco).
- Longitud del arco eléctrico.
- Angulo del electrodo respecto a la pieza.
- Velocidad de avance.
- Corriente eléctrica aplicada (amperaje).
Cuando se menciona que el soldador esté en la posición correcta, nos referimos a que se deberá estar en una posición estable y cómoda, preferentemente de pie y con libertad de movimientos (Fig. 1).
La metodología indica que los pasos correctos a seguir a manera de práctica son los detallados a continuación:
- Colocar el electrodo en el portaelectrodo.
- Tomar el mango portaelectrodo con la mano derecha en una posición cómoda.
- Sujetarse la muñeca derecha con la mano izquierda.
- Apoyar el codo izquierdo sobre el banco de soldadura.
- Alinear el electrodo con el metal a soldar.
- Usar el codo izquierdo como pivote y practicar el movimiento del electrodo a lo largo de la unión a soldar.
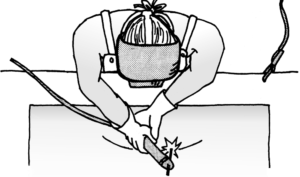
Cuando se menciona que el soldador deberá tener protección facial, nos referimos al uso de máscara o casco con lentes protectores. El mismo deberá cubrir perfectamente la cara y los ojos. Existen infinidad de modelos, sin embargo, para poder disponer de las dos manos en el proceso de soldadura, resultan ideales los cascos abisagrados, los que pueden colocarse en su posición baja con un ligero cabeceo (Fig. 2), lo que permite no alterar la posición del electrodo (de las manos) ante la pieza, previo al inicio de la soldadura.
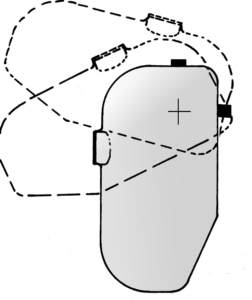
Ahora definiremos los cuatro factores importantes antes mencionados:
- Longitud del arco eléctrico: es la distancia entre la punta del electrodo y la pieza de metal a soldar. Se deberá mantener una distancia correcta y lo más constante posible.
- Angulo del electrodo respecto a la pieza: El electrodo se deberá mantener en un ángulo determinado respecto al plano de la soldadura. Este ángulo quedará definido según el tipo de costura a realizar, por las características del electrodo y por el tipo de material a soldar.
- Velocidad de avance: Para obtener una costura pareja, se deberá procurar una velocidad de avance constante y correcta. Si la velocidad es excesiva, la costura quedará muy débil, y si es muy lenta, se cargará demasiado material de aporte.
- Corriente eléctrica: Este factor es un indicador directo de la temperatura que se producirá en el arco eléctrico. A mayor corriente, mayor temperatura. Si no es aplicada la corriente apropiada, se trabajará fuera de temperatura. Si no se alcanza la temperatura ideal (por debajo), el aspecto de la costura puede ser bueno pero con falta de penetración. En cambio, si se trabaja con una corriente demasiado elevada, provocará una temperatura superior a la óptima de trabajo, produciendo una costura deficiente con porosidad, grietas y salpicaduras de metal fundido.
Para formar el arco eléctrico entre la punta del electrodo y la pieza se utilizan dos métodos, el de raspado o rayado y el de golpeado. El de rayado consiste en raspar el electrodo contra la pieza metálica ya conectada al potencial eléctrico del equipo de soldadura (pinza de tierra conectada). El método de golpeado es, como lo indica su denominación, dar golpes suaves con la punta del electrodo sobre la pieza en sentido vertical. En ambos casos, se formará el arco cuando al bajar el electrodo contra la pieza, se produzca un destello lumínico. Una vez conseguido el arco, deberá alejarse el electrodo de la pieza unos 6 mm para así poder mantenerlo. Luego disminuir la distancia a 3 mm (distancia correcta para soldar) y realizar la soldadura. Si el electrodo no se aleja lo suficiente, se fundirá con la pieza, quedando pegado a ella.
Ahora explicaremos como realizar costuras, ya que resultan básicas e imprescindibles en la mayor parte de las operaciones de soldadura. Los pasos a seguir son los siguientes:
- Ubicar firmemente las piezas a soldar en la posición correcta.
- Tener a mano varios electrodos para soldar. Colocar uno en el porta electrodo.
- Colocarse la ropa y el equipo de protección.
- Regular el amperaje correcto en el equipo de soldadura y encenderlo.
- Ubicarse en la posición de soldadura correcta e inicie el arco.
- Mover el electrodo en una dirección manteniendo el ángulo y la distancia a la pieza.
- Se notará que conforme avance la soldadura, el electrodo se irá consumiendo, acortándose su longitud. Para compensarlo, se deberá ir bajando en forma paulatina la mano que sostenga el porta electrodo, manteniendo la distancia a la pieza.
- Tratar de mantener una velocidad de traslación uniforme. Si se avanza muy rápido, se tendrá una soldadura estrecha. Si se avanza muy lento, se depositará demasiado material.
Resulta imprescindible realizar la máxima práctica posible sobre las técnicas de costuras o cordones. Una forma de autoevaluar si se consiguió tener un dominio del sistema de soldadura es realizar costuras paralelas sobre una chapa metálica. Si se logran costuras rectas que conserven el paralelismo sin realizar trazados previos sobre la chapa, se puede decir que ya se ha conseguido un avance apreciable sobre este tema.
Se debe tener un total dominio de las costuras paralelas (Fig. 3) para poder realizar trabajos de relleno (almohadillado) y/o reconstrucción, los que detallaremos más adelante.
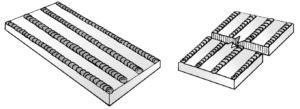
Cuando se aporta metal aplicando el sistema de arco protegido, resulta común querer realizar una soldadura más ancha que un simple cordón (sólo movimiento de traslación del electrodo). Para ello, se le agrega al movimiento de avance del electrodo (movimiento de traslación) un movimiento lateral (movimiento oscilatorio). Existen varios tipos de oscilaciones laterales (Fig. 4). Cualquiera sea el movimiento elegido o aplicado, deberá ser uniforme para conseguir con ello una costura cerrada, y así facilitar el desprendimiento de la escoria una vez finalizada la soldadura.
En la Fig. 4 se detallan los cuatro movimientos clásicos. De los movimientos ilustrados, el de aplicación más común es el mencionado con la letra A, aunque los movimientos C y D resultan más efectivos para realizar soldaduras en metales de mayor espesor.
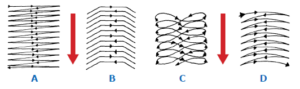
En la fotografía de la Fig. 5 se observan varias pruebas de soldadura realizadas con distintas corrientes y velocidades de avance. En ella, podemos clasificar a las soldaduras de la siguiente manera, a saber:
A. Costura correcta con amperaje y velocidad adecuados.
B. Costura aceptable con amperaje muy bajo.
C. Costura deficiente por amperaje muy elevado.
D. Costura aceptable con amperaje muy bajo, ocasionando demasiado aporte metálico.
E. Costura deficiente con corriente inadecuada.
F. Costura correcta con muy poca velocidad de avance. Observar que la costura está muy ancha y muy alta.
G. Costura deficiente con corriente adecuada pero con velocidad de avance muy elevada.
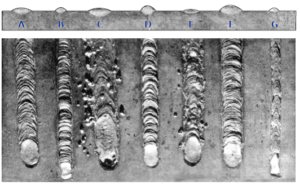
Existen también las llamadas técnicas de rellenado (almohadillado) o reconstrucción. Es importante tener un dominio de las técnicas explicadas hasta aquí porque el relleno y reconstrucción requiere de capas sucesivas de soldadura (Fig. 6). Para que el trabajo quede bien realizado, se deberá procurar evitar poros en las costuras en donde pueden quedar atrapados restos de escoria de la capa anterior.
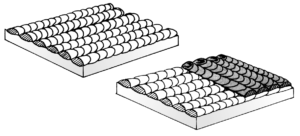
Esta técnica se utiliza en el relleno o reconstrucción de partes gastadas (ejes, vástagos, pistones, etc.). Se van sumando capas sucesivas de soldadura hasta llegar a la altura de relleno necesaria. Las capas entre sí deberán estar rotadas 90°, y de esta forma se logra una superficie más lisa y se limita la posibilidad de que queden poros en la capa de relleno. Cuando se realiza el relleno en las cercanías de los bordes de la pieza, el aporte de soldadura tiende a “derramarse”. Para evitar este efecto, se utilizan como límites placas de cobre o grafito sujetas al borde a rellenar. La placa puesta como límite no interviene ni se funde por los efectos del calor producido en el proceso de soldadura (Fig. 7).
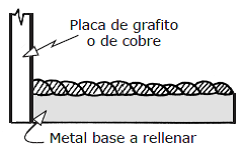
Este método resulta de suma utilidad para lograr bordes de relleno rectos, ahorrando bastante trabajo de mecanizado posterior.
Uniones básicas con arco protegido (SMAW)
Ahora que ya hemos explicado los procedimientos para depositar cordones y costuras, y para realizar reconstrucciones y rellenos, podemos aplicar estos conocimientos para realizar las uniones típicas en soldadura metálica con arco protegido. Estas son cinco (Fig. 8): A) la unión a tope, B) la unión en T, C) la traslapada, D) la unión en escuadra, y E) la de canto. Además de estas uniones, existen cuatro posiciones diferentes para realizarlas. Estas son la plana, la vertical, la horizontal, y sobre la cabeza. Estas posiciones se evidencian en la Fig.9, en la además se ilustran todas las variantes intermedias. A la soldadura que se deposita en una unión en T se la llama soldadura de filete. También frecuentemente, se le da este nombre a la unión.
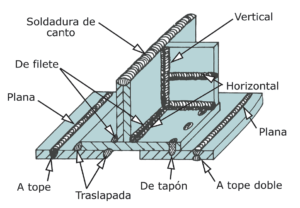
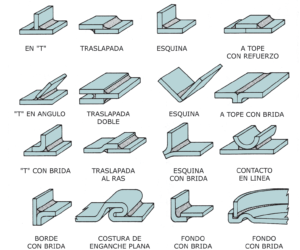
Referencias
[1] H.B. Cary, Modern Welding Technology, 2nd Ed., Prentice-Hall, 1989
[2] «Filler Metal Comparison Charts,» AWS FMC-89, American Welding Society
[3] «Safety in Welding and Cutting,» ANSI/AWS Z49.1, American Welding Society
[4] «Technical Guide for Shielded Metal Arc Welding,» Hobart Brothers Co.
[5] Rodríguez, P. Manual De Soldadura – Soldadura Eléctrica, MIG y TIG. 1ra Ed., Libreria y Editorial Alsina. Buenos Aires, Argentina.
[6] INDURA (2020). Manual de Sistemas y Materiales de Soldadura [Archivo PDF]. http://www.indura.cl/Descargar/Manual%20de%20Soldadura%20INDURA?path=%2Fcontent%2Fstorage%2Fcl%2Fbiblioteca%2F00da6ac5e6754e428ecd94f1c78711cb.pdf
Contacto: orlandoaco2@gmail.com