Autor: Pérez Luis. Unidad de Ensayos no Destructivos, Análisis de Fallas y Corrosión de Materiales. Centro de Tecnología de los Materiales (CTM). FIIIDT.
A medida que transcurre los años la instrumentación y el desarrollo del software ha ayudado a que la técnica del pulso eco (UT) sea más confiable en resguardo y control de calidad de los materiales y equipos. En un principio, la utilización del sonido para la detección de heterogeneidades, se basó en la medición de la caída de la intensidad acústica del haz ultrasónico cuando éste atraviesa zonas del material con presencia de discontinuidades. Las mismas fueron desarrolladas y aplicadas por Sokolov, en el año de 1929. [1] A partir de aquí surgió otros tipos de aplicaciones utilizando el sonido como base de trabajo, en 1945 gracias a la gran demanda de ensayos no destructivos, el ensayo por ultrasonido tuvo una total aceptación y comenzó un proceso de continuo de desarrollo de tecnologías y diversificación de las aplicaciones.
Desde hace muchos años el pulso eco convencional es ampliamente utilizado y a pesar de la aparición de tecnologías emergentes sigue siendo empleado en la inspección de materiales y equipos, continuando con lo expuesto en la parte I de esta nota técnica, se seguirán abordando conceptos básicos para la caracterización de las discontinuidades usando esta técnica.
Una discontinuidad en un objeto inspeccionado representa un obstáculo al ultrasonido, con lo que, la información sobre esta discontinuidad es obtenida por el ultrasonido reflejado por ella, (por su eco). [2] Por consecuencia al evaluar una discontinuidad nos basamos principal mentalmente en la reflexión que produce, es decir, el sonido que se propaga dentro del material, lo que genera cierta información de la pieza evaluada la cual solo el personal capacitado según la experiencia que tenga puede dar una respuesta confiable y un análisis preciso.
Entre los factores que afectan la evaluación de una discontinuidad se pueden mencionar:
- El poder de resolución.
- La condición superficial.
- La exactitud al determinar el ángulo de refracción.
- La pérdida de sensibilidad.
- La divergencia del haz ultrasónico.
- Las características de la discontinuidad.
- La capacitación, desempeño y experiencia del personal técnico.
Como es de notar, son diversos los factores que afectan el desempeño de la técnica, es necesario, además de tener el control sobre cada uno de estos, conocer qué tipo de discontinuidades se pueden encontrar al momento de realizar una inspección y esto depende, a manera general, en qué etapa se originó la discontinuidad:
- En fabricación, en la cual se podría obtener discontinuidades inherentes al de manufactura por el cual fue obtenido el material o componente.
- Y de servicio, en esta se puede encontrar grietas por esfuerzo, las cuales inician en puntos de altas concentración de energías. Se estima que un equipo que tiene partes en movimiento o que se encuentra sujeto a vibración, aproximadamente el 90% de las fallas presentes incluye a la fatiga de alguna forma. También obtenemos corrosión por deterioro de metales, debido a la acción química del medio circundante o contrayente y causar la falla de materiales sometidos a cargas estáticas debido a la reducción de la resistencia a la carga de la sección transversal.
TÉCNICAS DE DIMENSIONAMIENTO
Estas técnicas nos ayudan a identificar el tipo de discontinuidad y su morfología, en este sentido se tiene lo siguiente:
Uso de palpadores de haz angular [4]
Cuando un palpador de haz angular, que esté conectado a un equipo de ultrasonido, se acopla sobre la superficie de una placa, el haz de ondas longitudinales emitido por el cristal del palpador se refracta al atravesar la interface, convirtiéndose en un haz de ondas de corte. Éste haz se propaga en “zig-zag” a través de la placa como se ilustra en la figura N°1
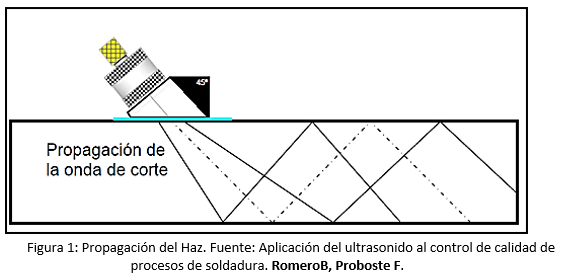
La reflexión en la esquina inferior del borde de la placa se efectúa a una distancia SD/2 (distancia de medio salto) y la distancia en que se genera la reflexión en la esquina superior de denomina SD (distancia de salto), veamos la figura Nº 2. Se vislumbra; dada la forma en “V” del recorrido del haz ultrasónico hasta completar la SD, se le denomina “trayectoria en V”.
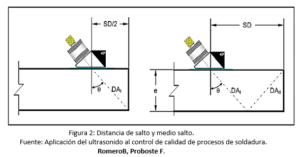
La distancia recorrida por el haz hasta la superficie inferior de la placa (DAI) se conoce como “primera pierna” de la trayectoria en “V”, y la distancia desde la superficie inferior hasta la superior (DAII) es la “segunda pierna” y así sucesivamente. Conociendo el ángulo de refracción del haz ultrasónico, marcado en el palpador; y el espesor se pueden calcular las distancias de salto y medio salto, como se aprecia en la figura N°3.
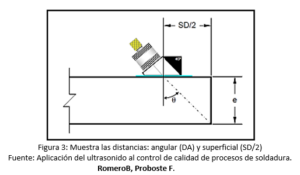
En consecuencia, de la figura anterior se deduce:

Por lo que despejando se obtiene:

Los palpadores angulares cuentan, para su ángulo de refracción, con el factor 2*tgq por lo cual, para conocer la distancia de salto y de medio salto es cuestión, únicamente, de conocer el espesor de la placa.
Ubicación de las discontinuidades usando el palpador de haz angular
Al verificar una placa con palpador de haz angular y se detecta una discontinuidad que por ejemplo, la discontinuidad de encuentra perpendicularmente en la dirección del haz ultrasónico podemos detectar con solo visualizarlo en la pantalla del osciloscopio la distancia angular, es decir, el recorrido del sonido dentro del material cuando se refleja en la discontinuidad, también en algunos equipos podemos obtener datos como la distancia superficial a la que se encuentra la discontinuidad y la profundidad de la misma. Como se ilustra en la figura N°4;
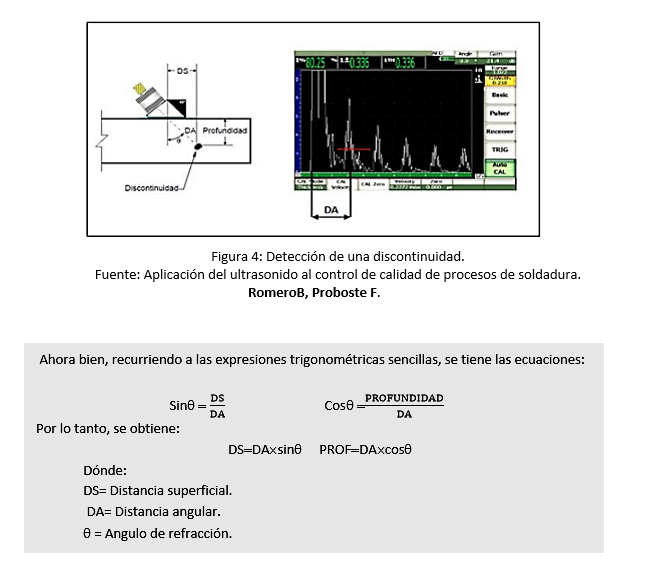
Inspección de un cordón de soldadura con palpador de haz angular
Al evaluar un cordón de soldadura es necesario realizar recorridos a lo largo de la soldadura y en movimientos donde se evidencie la estructura interna de la soldadura, es decir, si el sensor se encuentra en una posición donde solamente se visualice medio salto del haz ultrasónico el sensor deberá separase a una distancia donde se evalúe con el salto completo del haz ultrasónico, por ejemplo, si con el medio salto se puede evaluar la raíz de la soldadura con el salto completo podremos analizar la parte superior de la soldadura que sería el refuerzo de la soldadura. Como se ilustra en la figura N°5
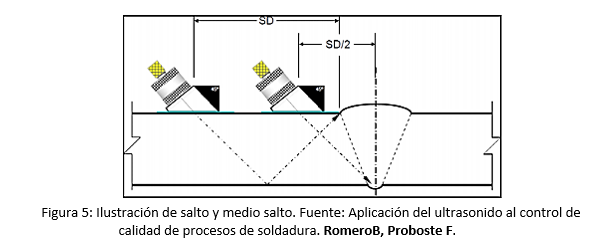
Método por caída de amplitud [4]
Al aplicar este método, normalmente es imperativo determinar la longitud de la discontinuidad para completar su evaluación. Para ello, se recurre a una técnica conocida como la “Técnica de caída de 6 dB”. Esta técnica consiste en lo siguiente:
Después de obtener la máxima amplitud de la indicación de una discontinuidad (maximización), se desplaza el palpador en una dirección, siguiendo la dirección en la que está orientada la discontinuidad, y se detiene el desplazamiento en el momento que la indicación de la discontinuidad sufra una caída de amplitud al 50%, con respecto a su amplitud máxima, lo que equivale a -6 dB.
La base de esta técnica es asumir que la indicación de la discontinuidad tiene una caída de amplitud a la mitad cuando la parte central del haz se encuentra en el extremo de la discontinuidad, esto es, que se está detectando el borde de la discontinuidad en ese punto.Después de marcar la posición de los puntos más alejados entre sí, entonces se puede determinar directamente la longitud de la discontinuidad, midiendo la distancia entre los puntos obtenidos, que corresponden a los extremos de la discontinuidad. Para determinar la longitud de discontinuidades pequeñas, se tiene menor exactitud que para discontinuidades grandes.
Método por caída de amplitud (para discontinuidades grandes).
Este método se basa en la “Técnica de caída de 6 dB” (caída al 50% de amplitud) que, como se mencionó, consiste en determinar la ubicación de los puntos donde la amplitud de las indicaciones equivale a la caída de 6 dB, con respecto a la amplitud máxima, cuando el palpador se mueve más allá de la posición en la que se obtiene la máxima amplitud de la indicación de discontinuidad, como se ilustra en la figura N°6. También conocido como “Método alrededor”, ya que se dibuja con buena exactitud el “contorno de una discontinuidad grande”.
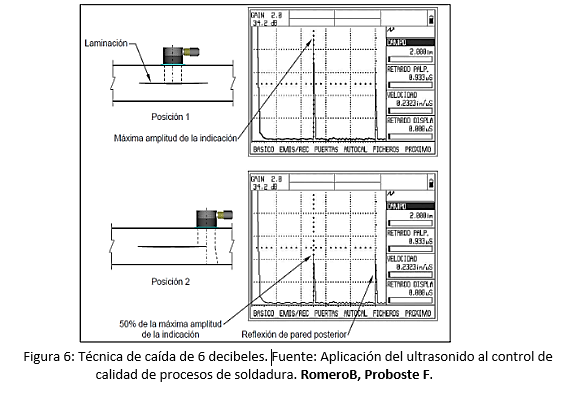
Análisis de las ecodinámicas de los reflectores
Para poder analizar una discontinuidad tenemos que determinar el comportamiento de la indicación al observarla en la pantalla AScan cuando el transductor es maniobrado y este es interceptado el haz ultrasónico por una discontinuidad.
A continuación se indican resultados obtenidos de la inspección por ultrasonido, correspondientes a diferentes análisis de probetas inspeccionadas en el laboratorio de ensayos no destructivos del centro de tecnología de materiales de la fundación instituto de ingeniería;
Defecto: Porosidad
Descripción: Producen un eco angosto y bien definido y puede ser detectado desde cualquier dirección. La indicación aparece a la misma distancia recorrida por el haz ultrasónico y muestra así la misma amplitud sin importar la dirección. La identificación de un grupo o cadena de poros es totalmente diferente. Las indicaciones individuales de los poros pueden ser integradas en una sola indicación en la pantalla y son fáciles de distinguir de indicaciones de inclusiones y grietas.
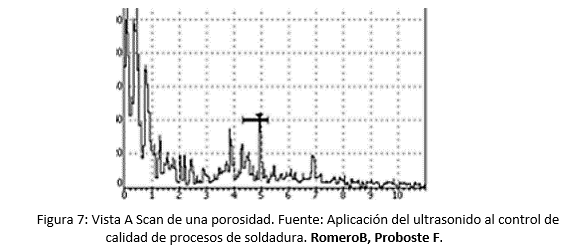
Defecto: Grietas
Descripción: Normalmente son cerradas, tienen lados tersos y producen indicaciones ultrasónicas de una gran amplitud. Cuando esta discontinuidad es perpendicular a la salida del haz ultrasónico es decir que se topa de frente con la discontinuidad, se asemeja mucho a la reflexión de una pared de fondo. Esto significa que el haz ultrasónico puede ser reflejado por la superficie y por la grieta y gracias a ello produce indicaciones de por lo menos el doble de amplitud comparadas con indicaciones de discontinuidades del mismo tamaño.
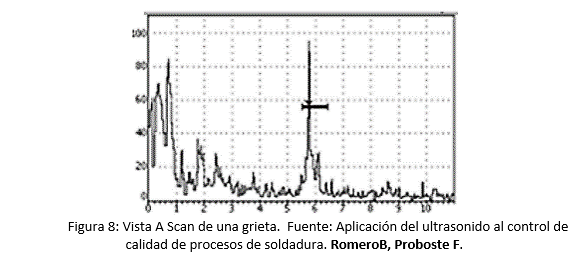
Defecto: Inclusión
Descripción: Las líneas e inclusiones de escoria producen indicaciones de mayor amplitud que las producidas por porosidad, ya que cuentan con una superficie reflectora mayor. La inclusión puede ser identificada observando la indicación ya que es posible ver el extremo de la misma.

En la tercera y última entrega de esta nota técnica se hará referencia a las experiencias llevadas a cabo en el laboratorio de ensayos no destructivos (END) del Centro de Tecnología de los Materiales (CTM) de la Fundación instituto de Ingeniería (FIIIDT).
Referencias
[1] https://imt.mx/
[2]. Pruebas no destructivas J. Correa. Disponible en: https://juliocorrea.files.wordpress.com/2007/10/pruebas-no destructivas.pdf
[3] Caracterización mediante técnicas de ultrasonido de un laminado de fibra de vidrio. Valencia J. Disponible en: https://e-archivo.uc3m.es/
[4] Aplicación del ultrasonido al control de calidad de procesos de soldadura RomeroB, Proboste F. Disponible en: http://repobib.ubiobio.cl/
Contacto: eduardo.20per.2013@gmail.com