Autores: Torres Víctor, Figueroa Andreina. Unidad de Ensayos no Destructivos, Análisis de Fallas y Corrosión. Centro de Tecnología de los Materiales. FIIIDT.
- INTRODUCCIÓN
Las fallas en componentes estructurales de una aeronave pueden tener catastróficas consecuencias, resultando en lamentables pérdidas humanas y materiales. La investigación de defectos y fallas son de vital importancia para la prevención de accidentes. Una falla ocurre cuando un componente no es capaz de soportar los esfuerzos a los que está sometido durante su funcionamiento. Las grietas a fatiga son las causas más comunes de fallas estructurales en aeronaves [1].
La corrosión y la corrosión fatiga son procesos que dependen de múltiples factores, tales como carga, material, medio ambiente entre otros. Las fallas a fatiga se inicien en sitios de alta vulnerabilidad, particularmente en áreas sujetas a esfuerzos dinámicos donde se localizan concentradores de esfuerzos. Los concentradores de esfuerzos pueden ser geométricos, metalúrgicos, o una combinación de ambos. Los concentradores de esfuerzos geométricos pueden ser cambios de forma como por ejemplo un escalón, cambios de diámetro, esquinas de gran ángulo y discontinuidades superficiales tales como muescas y marcas de maquinado. Los concentradores de esfuerzo metalúrgicos pueden ser, grietas de temple, picaduras, inclusiones, segundas fases etc. [2 y 3].
La microestructura juega un papel primordial en el inicio de la fractura y a propagación de la grieta que causa la falla del componente. Frecuentemente las grietas de fatiga ocurren cerca de la superficie libre, donde los esfuerzos nominales son a menudo mayores. Este estudio se enfocó en la determinación del origen y causas de falla de un tren de aterrizaje. Ver figura 1
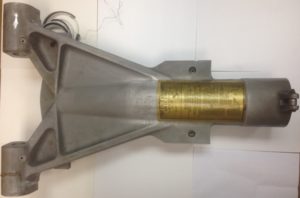
- TÉCNICAS EXPERIMENTALES.
La metodología empleada consistió en la caracterización del tipo de fractura, utilizando inspección visual y observación detallada de la superficie de fractura del asiento del retén metálico (Ver figura 2). Mediante estéreo lupa y microscopio electrónico de barrido con identificación de las posibles zonas de iniciación y propagación hasta la fractura final.
Así mismo se caracterizó químicamente el material de fabricación del asiento del retén mediante análisis químico por espectroscopia de absorción atómica.

3. RESULTADOS Y DISCUSIÓN.
3.1 Inspección Visual.
3.1.1 Reten metálico.
La inspección visual del retén metálico, identificado como # 17 (ver figuras 3 y 5) reveló:
1.- Presencia de deformación plástica post fractura.
2.- Marcas de fricción entre el asiento y el retén.
3.- Perdida parcial del recubrimiento en la cara interna con registro de picaduras.
4.- Perdida total del Recubrimiento en la cara externa (figura 4).
5.- Presencia de picaduras en el metal expuesto de la cara externa.
3.1.2 Superficie de fractura.
La superficie de fractura exhibe una apariencia frágil. Observándose macroscópicamente lisa y suave. El inicio múltiple de grieta (figura 6 y 7) es claro: Son varios los sitios del asiento en los que las picaduras actúan como concentradores de esfuerzo local, permitiendo la formación, el avance de grietas y su consecuente detención dejando a su paso la maraca característica. En el momento en que hay varios frentes de grieta avanzando [3], la capacidad de trasmisión de carga disminuye a tal punto que el resto del material se separa por sobrecarga, de allí la diferencia de aspecto en la superficie de fractura y las zonas 1 y 2 de la figura 6.Lacorrosion toma lugar simultáneamente con los esfuerzos tensiles fluctuantes, este efecto combinado es lo que se conoce con el nombre de corrosión fatiga. Por los que el mecanismo de falla del tren de aterrizaje es corrosión fatiga. Las picaduras actúan como iniciadores de la falla y el modo de propagación de grieta es Fatiga. [4].
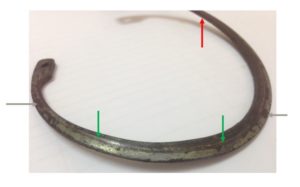
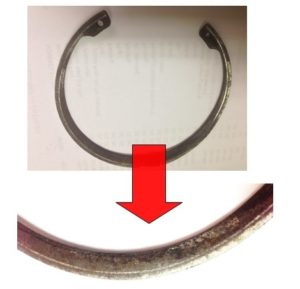
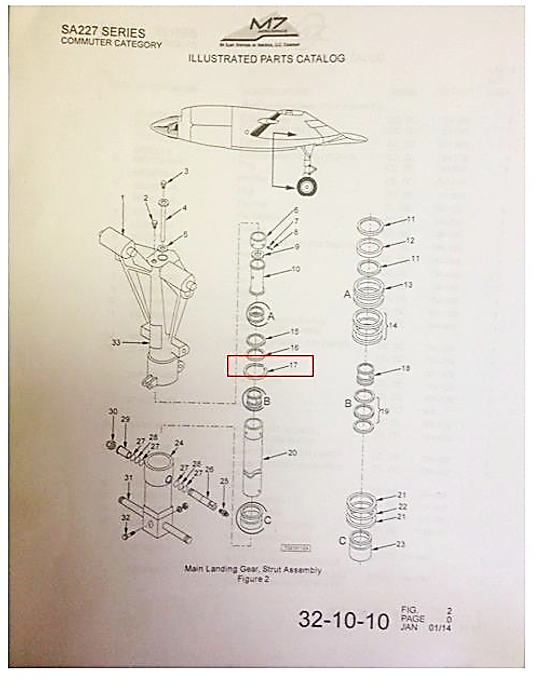
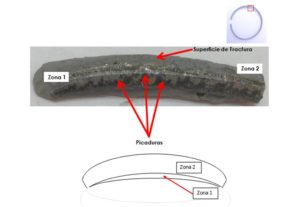

3.2 Análisis químico
Se extrajeron cuidadosamente virutas del tren de aterrizaje bajo estudio, para ser sometidas a Espectroscopía de Absorción Atómica. Los resultados son reportados en la Tabla adjunta.
A partir de los resultados de composición química obtenidos, el material de fabricación del Tren de Aterrizaje bajo estudio es muy similar a una Aleación de Aluminio de la serie 7XXX, específicamente una 7075.
3.3 Ensayo de dureza
Se realizó un barrido de dureza, empleando un durómetro Wilson Rockwell SERIE 2000, en la tabla adjunta se reportan los valores así obtenidos en HRB (Dureza Rocwell B) y sus equivalencias en HB (Dureza Brinell).
3.4 Análisis Metalográfico.
Para descartar cualquier característica metalúrgica asociada a la falla, se practicaron dos (2) cortes para el estudio metalográfico: uno cercano al inicio de la fractura y otro alejado de ésta. Fueron preparados metalográficamente bajo el procedimiento de la norma ASTM E3-11, desbastados, y pulidos, el registro fotográfico corresponde a la Figura 8, en que es evidente la presencia de picaduras. Posteriormente, los cortes son atacados químicamente con el reactivo Keller (2 ml de HF (48%), 3 ml de HCl (concentrado), 5 ml HNO3 (concentrado), 190 ml de H2O), lo que permitió su observación bajo un microscopio óptico NIKON modelo EPIPHOT.
La microestructura revelada es dendrítica celular típica de una condición de colada (figura 9), corresponde a un aluminio 7075, y no se detectaron elementos metalúrgicos que pudieran estar asociados a la falla. El tratamiento térmico corresponde a un envejecimiento artificial [5].
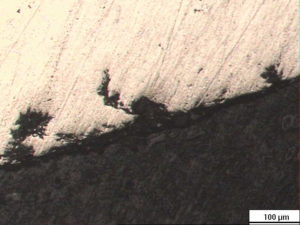
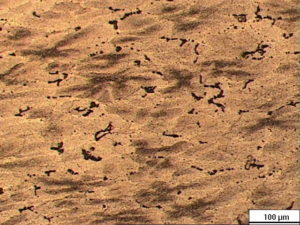
3.5 Microscopia electrónica.
La Figura 10 corresponde a una sección de la superficie de fractura de uno de los inicios de grieta: claramente diferenciable las Zonas 1 y 2 sección, acompañada de los detales dé cada zona con sus respectivos análisis químicos semicuantitativos por dispersión de energía de rayos X (EDS). Los resultados son coincidentes con el sistema bajo estudio, excepto los elementos sodio (Na) y cloro (Cl), siendo el cloro elemento foráneo y agresor al material de fabricación del asiento. La presencia del Cl sobre la superficie es indicativo que permaneció un tiempo expuesta a la atmosfera agresiva.
Micrografías a mayor magnificación de la superficie de fractura; sobre la Zona 1 específicamente, revela la presencia de estriaciones de fatiga[6], indicando propagación bajo ciclos de carga alternos.
Los registros de los análisis químicos semicuantitativos por dispersión de energía de rayos (EDS) de las picaduras detectadas en el asiento del retén (Ver Figura 6) corresponden a las Figuras 11. Una sección del retén metálico también fue analizada, sobre su superficie se registran elementos que corresponde a un acero de baja aleación además del elemento Cloro, que es agresor a dicho sistema (Ver Figuras 12).
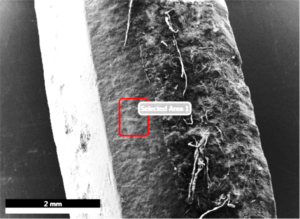
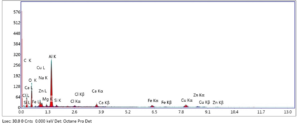
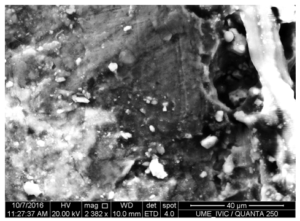
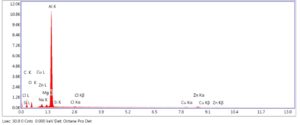
- CONCLUSIONES
- El mecanismo de falla del tren de aterrizaje es Corrosión Fatiga
- Los iniciadores de grieta son picaduras generadas por la presencia de cloro (Cl) proveniente del medio ambiente, éstas actúan como concentradores de esfuerzo local, iniciando las grietas.
- El material de fabricación del tren de aterrizaje es muy similar a una aleación de aluminio 7075 T6.
- BIBLIOGRAFIA
[1] Harmon ND. Why aircraft Fail. Mater Today 2002.
[2] P.Shi, S. Mahadevan. Corrosion Fatigue and multiple site damage reliability analysis. International Journal of Fatigue 25 (2003) 457-469.
[3]Osman Asi, Onder Yesil. Failure analysis of an aircraft nose landing gear piston rod end. Engineering Failure Analysis 32 (2013) 283-291.
[4] Lincoln JW. The USAF approach to attaining structural integrity of aging aircraft. IN: Cahng CI, Sun CT, editors. Structural integrity in aging aircraft. AD-vol. 47. New York: ASME: 1995.
[5] Metals Handbook. Ninth Edition. Vol 8. Metallography and Microstructure.
[6] Metals Handbook. Ninth Edition. Vol 11.Failure Analysis and Prevention. 1986. ASM.
Contacto: torrespvictorj@gmail.com