Autores: Edgar Pérez, José Antonio País, José Padilla, Misael Coste. Centro de Ingeniería Mecánica y Diseño Industrial (CIMECDI). FIIIDT.
La Soldadura por Arco de Metal Protegido (Shielded Metal Arc Welding – SMAW) en inglés, comúnmente llamada Electrodo Revestido o Varilla, es un proceso de soldadura manual mediante el cual se genera un arco entre un electrodo consumible cubierto de fundente y la pieza de trabajo. El proceso utiliza la descomposición de la cubierta de fundente para generar un gas protector y para proporcionar elementos fundentes para proteger las gotas de metal de soldadura fundido y el baño de soldadura.
El proceso SMAW:
Las características importantes del proceso SMAW se muestran en la Fig. 1. El arco se inicia al tocar momentáneamente o «rayar» el electrodo en el metal base. El arco resultante derrite tanto el metal base como la punta del electrodo de soldadura. El metal / fundente del electrodo fundido se transfiere a través del arco (por las fuerzas del arco) a la piscina de metal base, donde se convierte en el depósito de soldadura cubierto por la escoria protectora menos densa de la cubierta del electrodo.
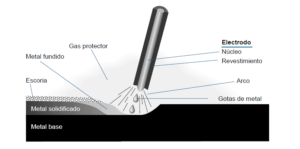
Ventajas y limitaciones:
El proceso SMAW es el proceso de soldadura más utilizado. Es el más simple, en términos de los requisitos de equipo, pero es, quizás, el más difícil en términos de capacitación de soldadores y requisitos de nivel de habilidad.
Aunque el nivel de habilidad del soldador es una preocupación, la mayoría de los soldadores que ingresan al campo comienzan como «soldadores de varilla» y desarrollan las habilidades a través de la formación y la experiencia. La inversión en equipo es relativamente pequeña y los electrodos de soldadura (excepto en metales muy reactivos, como titanio, magnesio y otros) están disponibles para prácticamente toda la fabricación, construcción, o aplicaciones de mantenimiento. La soldadura por arco de metal blindado tiene la mayor flexibilidad de todos los procesos de soldadura, porque se puede utilizar en todas las posiciones (plano, vertical, horizontal y elevado), con prácticamente todos los espesores de metal base (1,6 mm, o 1/16 in., y mayores), y en áreas de accesibilidad limitada, que es una capacidad muy importante.
Debido a que el proceso SMAW es básicamente un proceso manual, el nivel de habilidad del soldador es de suma importancia para obtener una soldadura aceptable. El ciclo de trabajo del soldador es generalmente bajo, debido a la pausa de trabajo incorporada, que se produce después de que cada electrodo se consume y requiere reemplazo. Además de reemplazar el electrodo cuando se detiene el arco (roto), el soldador puede «astillarse» o quitar la escoria y limpiarla del área de inicio y soldadura con un cepillo de alambre para permitir la deposición adecuada de la soldadura posterior. Esta operación de limpieza y reemplazo de electrodos ocurre muchas veces durante la jornada laboral (aproximadamente cada dos minutos, o el tiempo que generalmente se tarda en consumir un electrodo). Esta parada de astillado, de cepillado de alambre y del reemplazo de electrodos evitan que el soldador logre un factor de operador o ciclo de trabajo, eso es mucho mayor que el 25%.
Calidad de soldadura:
La calidad de la soldadura depende del diseño y accesibilidad de la junta, así como del electrodo, la técnica y la habilidad del soldador [7]. Si los detalles de las juntas varían mucho de los detalles de diseño establecidos, entonces puede resultar una soldadura. Otros factores que también reducen la calidad son la limpieza inadecuada entre cordones, la mala ubicación de la soldadura individual perlas dentro de la articulación y varios problemas con los electrodos individuales, incluido el flujo y los cables del núcleo que faltan parcialmente que no están centrados dentro de la cubierta de flujo. En general, se pueden obtener soldaduras de excelente calidad con el SMAW proceso, como lo demuestra su uso para unir secciones de casco submarino a presión y tuberías de petróleo / gas de alta presión.
Los espesores del metal base que se pueden soldar utilizando el proceso SMAW generalmente oscilan entre 1,6 mm (1/16 in.) hasta un espesor ilimitado. Los materiales más delgados requieren un soldador experto, un ajuste firme y la soldadura adecuada de diámetro pequeño de electrodo. La posición de soldadura también es importante para determinar los espesores mínimos de placa que se pueden soldar. Las soldaduras a tope de posición plana y las soldaduras de filete horizontales generalmente se consideran las más fáciles de soldar. Soldadura fuera de posición (vertical, por encima de la cabeza) requiere una mayor habilidad.
Circuito de soldadura:
El diagrama del circuito para el proceso SMAW se muestra en la Fig. 2. El equipo consta de una fuente de energía, portaelectrodos y cables de soldadura que conectan la fuente de energía al portaelectrodos y la pieza de trabajo.
Se puede utilizar corriente alterna (CA) o corriente continua, electrodo negativo (DCEN), o corriente continua, electrodo positivo (DCEP), dependiendo de las características del recubrimiento del electrodo. La fuente DCEN también se llama polaridad directa de CC, mientras que la fuente DCEP también se denomina polaridad inversa de CC. [7]
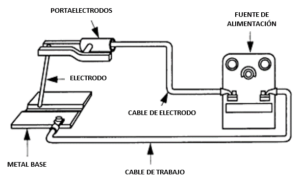
Equipo:
La máquina de soldar, o fuente de energía, es lo crucial del proceso SMAW. Su propósito principal es proporcionar energía eléctrica de corriente y voltaje adecuados para mantener un arco de soldadura controlable y estable. Las características de su salida deben ser del tipo de corriente constante (CC). Los electrodos SMAW operan dentro del rango de 25 a 500 A. El fabricante de electrodos debe sugerir un rango óptimo estrecho para cada tamaño y tipo de electrodo. Voltaje de arco operativo varía entre 15 y 35 V.
El portaelectrodo, que es sostenido por el soldador, sujeta firmemente el electrodo y le transmite la corriente de soldadura. Los portaelectrodos están disponibles en varios diseños, como el tipo pinza y coronilla, o tipo recodo, que se muestran en la Fig.3.
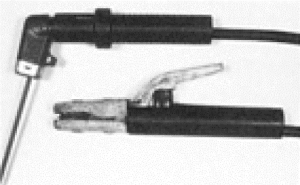
Cada estilo tiene sus proponentes y la selección suele ser una preferencia personal. Los portaelectrodos se designan por su capacidad actual. Los factores de selección, como la clasificación de corriente, el ciclo de trabajo, el tamaño máximo del electrodo y el tamaño del cable, se muestran en la Tabla 1. Por lo general, se desea el soporte más liviano que se adapte al tamaño de electrodo requerido.
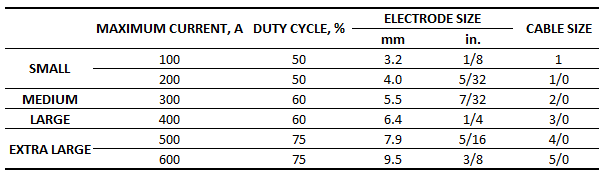
Todos los portaelectrodos deben estar completamente aislados. Debido a que se utilizan cerca del arco y están expuestos a altas temperaturas, se deteriorarán rápidamente. Es extremadamente importante mantener los portaelectrodos para asegurar que conserven su eficiencia de transporte de corriente, sus cualidades aislantes y su acción de agarre de electrodos. Los fabricantes suministran piezas de repuesto para que los soportes se puedan reconstruir y mantener para un funcionamiento seguro y eficiente.
Ciertos equipos auxiliares se pueden usar con el proceso SMAW, como los circuitos de control de bajo voltaje, que permiten cortar el voltaje de circuito abierto relativamente alto hasta que el electrodo toca la pieza de trabajo. Otros elementos incluyen interruptores de control remoto para los contactores, dispositivos de ajuste de corriente de control remoto y controladores de ralentí del motor para fuentes de energía impulsadas por motor.
Aplicaciones:
La mayoría de las operaciones de fabricación que requieren soldadura se esforzarán por utilizar los procesos mecanizados que ofrecen mayor productividad, mayor calidad y, por lo tanto, una producción más rentable. Por estas razones, el proceso SMAW ha sido reemplazado donde sea posible. Sin embargo, la simplicidad y capacidad del proceso SMAW para lograr soldaduras en áreas de accesibilidad restringida significa que todavía encuentra un uso considerable en ciertas situaciones y aplicaciones [7]. La construcción pesada, como la construcción naval y la soldadura «en el campo», lejos de muchos servicios de apoyo que proporcionarían gas protector, agua de enfriamiento y otras necesidades, dependen en gran medida del proceso SMAW.
Aunque el proceso SMAW encuentra una amplia aplicación para soldar prácticamente todos los aceros y muchas de las aleaciones no ferrosas, se utiliza principalmente para unir aceros. Esta familia de materiales incluye aceros bajos en carbono o suaves, aceros de baja aleación, aceros de alta resistencia, aceros templados y revenido, aceros de alta aleación, aceros inoxidables y muchos de los hierros fundidos. El proceso SMAW también se utiliza para unir níquel y sus aleaciones y, en menor grado, el cobre y sus aleaciones. Puede usarse, pero rara vez se usa para soldar aluminio. Además de unir metales, el proceso SMAW se utiliza con frecuencia para la superficie protectora de metales base. El depósito de revestimiento se puede aplicar con el propósito de controlar la corrosión o la resistencia al desgaste (revestimiento duro).
Electrodos:
Los electrodos utilizados en el proceso SMAW tienen muchas composiciones diferentes de alambre de núcleo y una amplia variedad de tipos y pesos de cubiertas de fundente. Los diámetros estándar de los electrodos del cable central varían de 1,6 a 8 mm (1/16 a 5/16 in.).
La longitud del electrodo suele oscilar entre 230 y 455 mm (9 y 18 in.); las longitudes más cortas están asociadas con los electrodos de menor diámetro. Se proporciona un extremo desnudo y sin revestimiento del electrodo (el extremo de agarre) para hacer contacto eléctrico en el portaelectrodo.
El revestimiento del electrodo tiene numerosas funciones. Proporciona:
- Gas (normalmente, dióxido de carbono), de la descomposición de ciertos ingredientes de recubrimiento para proteger el arco y la zona de soldadura de la atmósfera.
- Desoxidantes, para eliminar y purificar el metal de soldadura depositado.
- Formadores de escoria, para proteger el metal de soldadura depositado de la atmosférica.
- Oxidación y para ayudar a formar el cuello de soldadura.
- Elementos ionizantes, para hacer el arco más estable y operar con corriente alterna.
- Aleación de elementos, para proporcionar características especiales al depósito de soldadura.
- Hierro en polvo, en ciertos electrodos, para aumentar la productividad para soldar metales ferrosos.
La American Welding Society (AWS) ha establecido un sistema para identificar y clasificar los diferentes tipos de electrodos de soldadura. Todos los electrodos SMAW tienen el prefijo E para indicar el electrodo de soldadura. Los símbolos que siguen al prefijo se basan en los criterios que mejor describen las capacidades de soldadura del metal del electrodo. Estos criterios incluyen la composición química del metal de soldadura depositado, las propiedades mecánicas del metal de soldadura, ciertos parámetros del proceso o combinaciones de todos los factores.
Electrodos recubiertos de acero suave y de baja aleación. El prefijo utilizado para identificar estos electrodos va seguido de una serie de números que indica el nivel mínimo de resistencia, la capacidad de posición y el tipo de cobertura y corriente de soldadura. Tabla 2 explica cómo se utiliza la serie de números en AWS A5.1, la especificación para electrodos de acero al carbono para soldadura por arco de metal blindado y AWS A5.5, la especificación para electrodos de acero de baja aleación. Los dos primeros dígitos después de la E en el electrodo E6010 designan una resistencia a la tracción de al menos 430 MPa (62 ksi) para el metal depositado en la condición de soldado. El tercer dígito indica la posición en la que se pueden realizar soldaduras satisfactorias con el electrodo. Así, el 1 en E6010, por ejemplo, significa que el electrodo es satisfactorio para su uso en todas las posiciones (plano, vertical, horizontal y por encima de la cabeza). El 2 en E6020 indica que el electrodo es adecuado para la posición plana y los filetes horizontales. El último dígito o los dos últimos dígitos, tomados en conjunto, indican el tipo de corriente aplicable que se utilizará y el tipo de recubrimiento del electrodo.
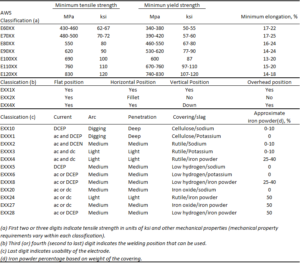
Electrodos cubiertos de acero inoxidable. El número de tres dígitos que sigue al prefijo E indica la composición química. Además, se pueden utilizar letras o números para indicar modificaciones de composición o facilidad de uso de la posición. La especificación AWS A5.4 identifica y clasifica electrodos de soldadura de acero al cromo y al cromo-níquel resistentes a la corrosión cubiertos.
Aleaciones de níquel y cobre. Las designaciones para las clasificaciones de productos no ferrosos, como níquel y aleaciones de níquel en AWS A5.11 y cobre y aleaciones de cobre en AWS A5.6, siguen el prefijo con una lista de abreviaturas de elementos químicos que son importantes para identificar la composición del producto, como ENiCu , EniCrFe, EcuSi y EcuNi.
Electrodos de soldadura de superficie. Las designaciones de estos productos se encuentran en las especificaciones AWS A5.13 y A5.21. Son muy similares al sistema utilizado para identificar electrodos no ferrosos.
Aluminio y aleaciones de aluminio. La especificación para electrodos de soldadura por arco de aluminio y aleación de aluminio, AWS A5.3, utiliza el prefijo E para indicar un electrodo cubierto, seguido de una serie de números que identifican la composición química que es equivalente a las designaciones de aleación de la Asociación de Aluminio (por ejemplo, E1100 , E3003 y E4043).
Los símbolos de sufijo se utilizan en varias clasificaciones. La especificación AWS A5.5 para metales de aportación de baja aleación utiliza sufijos como –A1, -B2, -B2L y –C1 para indicar composiciones químicas. La Tabla 3 identifica la composición química del depósito de soldadura asociada con varios sufijos que se encuentran en los electrodos de baja aleación. Las clasificaciones para productos no ferrosos en la especificación AWS A5.6 para aleaciones de cobre y en la especificación AWS A5.11 para aleaciones de níquel enumeran un sufijo de letra o número que indica la posición en una serie de agrupaciones de aleaciones similares. También se utiliza un patrón de sufijo similar en las especificaciones AWS A5.13 y AWS A5.21 para electrodos de soldadura de superficies. Electrodos de acero inoxidable cubiertos emplean un número, -15 o -16, como sufijo para identificar la usabilidad. El sufijo -15 indica que el electrodo está diseñado para operación en todas las posiciones usando corriente eléctrica DCEP. El sufijo -16 indica el funcionamiento en todas las posiciones con CA o DCEP.
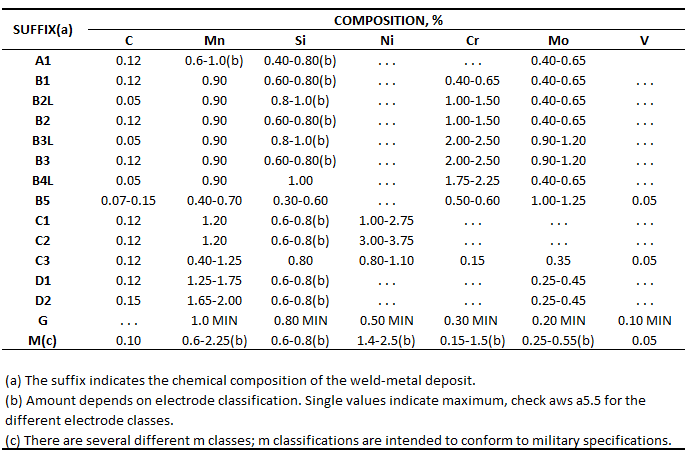
Tasas de deposición. La velocidad de fusión del electrodo está directamente relacionada con la corriente de soldadura. La densidad de corriente en el electrodo aumenta con una corriente más alta, lo que aumenta la velocidad de fusión, lo que, a su vez, aumenta la velocidad de deposición.
El recubrimiento del electrodo también afecta la tasa de deposición. Los tipos de polvo de hierro están diseñados para tener tasas de deposiciones más altas y, por lo tanto, mayor productividad. La Figura 4 muestra la tasa de deposición esperada versus el amperaje para varios electrodos en un ciclo de trabajo del 100%. (La tasa de deposición real será considerablemente menor. La tasa de deposición es una función del ciclo de trabajo, que se ve afectado por el tiempo empleado en cambiar los electrodos, limpiar la escoria de la soldadura, etc.) Tamaño del electrodo y, por lo tanto, rango de corriente utilizable están determinadas por el espesor del metal base, la posición de soldadura, el nivel de habilidad del soldador y los detalles de la unión.
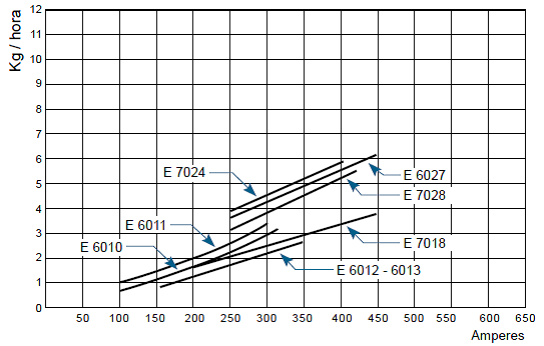
En el siguiente articulo Parte II, profundizaremos en las técnicas de soldadura eléctrica.
REFERENCIAS BIBLIOGRAFICAS
[1] H.B. Cary, Modern Welding Technology, 2nd Ed., Prentice-Hall, 1989
[2] «Filler Metal Comparison Charts,» AWS FMC-89, American Welding Society
[3] «Safety In Welding And Cutting,» ANSI/AWS Z49.1, American Welding Society
[4] «Technical Guide For Shielded Metal Arc Welding,» Hobart Brothers Co.
[5] Rodriguez, P. Manual De Soldadura – Soldadura Eléctrica, MIG y TIG. 1ra Ed., Librería y Editorial Alsina. Buenos Aires, Argentina.
[6] INDURA (2020). Manual de Sistemas y Materiales de Soldadura [Archivo PDF].
[7] Proceso SMAW: https://www.slideshare.net/VinicioAcuna/proceso-smaw
Contacto: orlandoaco2@gmail.com