Autores: Edgar Pérez, José Antonio Pais, José Padilla, Misael Coste / Centro de Ingeniería Mecánica y Diseño Industrial (CIMECDI) – FIIDT.
Objetivo.
La presente guía describe las actividades que deben efectuarse para la recolección de la información necesaria que permita la estimación de los tiempos necesarios para la realización del servicio de ingeniería de reversa (IR) en la parte correspondiente al modelaje sólido, para partes, conjuntos o equipos.
Alcance.
La estimación de tiempo comprende las actividades del proceso de ingeniería de reversa correspondiente a la preparación del equipo a analizar, medición o escaneo, post procesamiento de la malla poligonal, ingeniería de reversa del proceso de modelado, obtención del modelo tridimensional y el diseño de los planos a imprimir correspondientes a las partes modeladas, subconjuntos de partes y equipos a ser analizados.
- Definiciones.
- Escaneo. Es proceso mediante el cual se analiza un objeto para reunir datos de su forma. La información obtenida se usa para construir modelos digitales tridimensionales.
- Malla Poligonal (Polymesh). Es una superficie creada mediante un método tridimensional generado por sistemas de vértices posicionados en un espacio virtual con datos de coordenadas propios.
- Principios generales del procedimiento.
- Durante el proceso de ingeniería de reversa se deben completar diferentes actividades entre las que se encuentran el modelado de las partes y componentes del equipo bajo estudio.
- El modelado está basado en el dimensionamiento de las piezas, que puede realizarse en forma convencional (determinación de las características dimensionales con instrumentos de medición convencionales) o mediante el escaneo de las superficies de la misma.
- Dependiendo de sus dimensiones, características geométricas y número de componentes de las partes a ser modeladas, se puede estimar el tiempo y recursos necesarios para la realización de la fase de modelado y diseño de sus respectivos planos.
- A partir de las dimensiones y características geométricas de las piezas se define una escala para catalogar el nivel de complejidad de las partes. Este último nos define la metodología de captación de datos requerida para el dimensionamiento.
- Los niveles de complejidad descritos en la escala son:
A)- Estándar
B)- Básico
C)- Regular
D)-Complejo
E)- Muy complejo
- La metodología para la captación de datos se puede hacer de varias formas: Solo convencional, solo de escáner, mixta (uso de instrumentos convencionales y escáner), y con apoyo adicional de un centro de medición por coordenadas.
- Las dimensiones y peso de las partes a ser modeladas afectan este tiempo, aumentando la estimación inicial del tiempo en forma proporcional a la magnitud de estas características.
- Previo a la actividad de toma de datos dimensionales y geométricos, las partes a ser evaluadas deben de estar debidamente identificadas y codificadas de acuerdo a lo indicado en los anexos A “Clasificación del nivel de complejidad de las partes a ser modeladas” y B “Codificación”, del presente documento.
- Procedimiento.
- Desensamble, clasificación y codificación de partes.
- Análisis de funcionamiento. Se hace una inspección detallada del equipo o parte a ser estudiada. Se debe hacer un análisis exhaustivo de su funcionamiento con registros fotográficos y de video detallado, en modo estático y en modo de operativo, en todas las variantes y posiciones de referencia o finales de carrera, cada modo o posición que sea definida por el ciclo operativo del equipo o al que sea sometida la parte. Ver fig. 1 y 2.
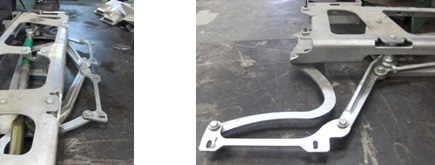
- Clasificación. Posterior al análisis de funcionamiento, en caso de que el objeto del servicio sea un equipo, se debe hacer una clasificación del mismo en sub ensambles que pueden ser agrupados de acuerdo a su funcionalidad como parte de la máquina o como sistema perteneciente a la misma. Esta clasificación se tomará en cuenta como en la codificación de las partes. Ver fig. 3.
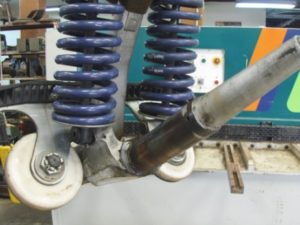
- Desensamble. Se procede con el desensamble del equipo en subconjuntos, para posteriormente continuar con el desensamble de cada subconjunto llegar hasta las partes individuales. Toda esta actividad debe ser registrada fotográficamente en el mismo orden de ejecución del desarme. Ver fig. 4.
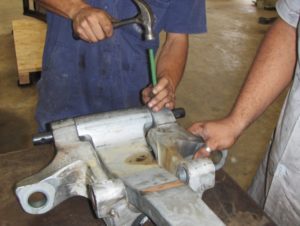
- Codificación. Después del desensamble, se procede con la codificación, clasificación de complejidad y clasificación de simetría de cada una de las partes individuales de acuerdo al sistema de descrito en los anexos 3 y 4, que se encuentran al final de este procedimiento. La información con el código debe ser añadida a cada pieza en un medio removible (etiquetas, adhesivo suave, etc.). Se debe hacer otro registro fotográfico individual de las partes por cada subconjunto, con la información de identificación perfectamente visible. Este catálogo fotográfico de las partes ya codificadas se usa para las actividades de Elaboración de lista de partes y Vaciado de la información en las tablas de estimación de tiempos. Ver fig. 5.
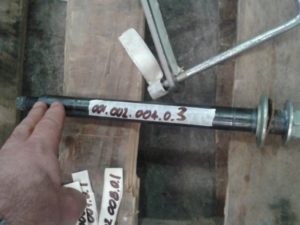
- Elaboración de listas de partes. Los datos relativos a la pieza (nombre, cantidad, proyecto, número de parte, subconjunto, simetría, nivel de complejidad y fotografía correspondiente) se registran en el formato de “Lista de partes” de acuerdo al análisis del número de características de cada parte del equipo y de acuerdo a la descripción de los niveles de complejidad ya definidos.
- Estimación del trabajo de Ingeniería Reversa, Modelado y Planos.Vaciado de la información en las tablas de estimación de tiempo. Los datos de la “Lista de partes” se transcriben en el archivo de Excel “Tablas para Estimación de tiempos”. Este libro tiene una (1) hoja de cálculo para cada nivel de complejidad (con un total de cinco hojas). Las formulas y factores para la estimación de los tiempos por actividad están adaptados a las tareas que deben ejecutarse para realizar el escaneo y modelado en cada uno de los casos. El llenado de la misma es mediante la ejecución de un macro. En cualquiera de las hojas de cálculo de este archivo, se cliquea sobre el botón “Formulario de estimación de tiempos” y aparece una ventana solicitando los datos necesarios. La información a introducir comprende: número de parte, código de la pieza de acuerdo a sistema de codificación ya explicado, número de características específicas de la parte. Una vez introducidos los datos requeridos se cliquea el botón “Ingresar código” y de acuerdo al nivel de complejidad especificado, los datos se introducirán en forma automática en la hoja correspondiente. En las columnas adyacentes se muestran los tiempos estimados para cada actividad dependiendo del nivel de complejidad y de las tareas a completar. Cuando se finalice la introducción de la información se debe cliquear en el botón “Salir del formulario”, cerrándose la ventana del mismo.Determinación de tiempos acumulados por actividad. La hoja de cálculo indica los acumulados de cada pieza por nivel de complejidad que posteriormente se utilizan para la planificación del trabajo y la distribución de los recursos disponibles.
- Revisión de los factores de estimación de tiempos del formulario. Se debe efectuar una revisión de los factores para la estimación de tiempos cada seis meses. Los factores utilizados para el cálculo se utilizan en una formula lineal dependiente de los promedios de los tiempos reales registrados durante la ejecución de la actividad en piezas tipo, divididos por el número de características de las piezas escaneadas/modeladas. Para el cálculo de los tiempos promedios, obtenidos de los registros reales de las actividades realizadas por primera vez, solo se utilizaron los tiempos registrados cuya diferencia con el tiempo estimado derivado del uso de un factor promedio temporal que incluye a todas las piezas escaneadas/modeladas, no fuese mayor al 100% por arriba y al 50% por debajo (estimado mayor al real en 100% o menor al real en un 50%). Luego de descartar los tiempos estimados que resultasen superiores al límite mayor e inferiores al límite menor, se recalcula el factor promedio de los registros que queden. Este factor por actividad y por nivel de complejidad es el que se introduce en la tabla donde se encuentra el valor de estos factores. Solo se hace una iteración. En las tablas de estimación se pueden observar las fórmulas y los factores utilizados.
Esta revisión periódica es necesaria de manera de ajustar los factores a valores que permitan estimaciones más exactas que solo se obtendrán superados el periodo de aprendizaje del manejo de la tecnología.
- Anexos.
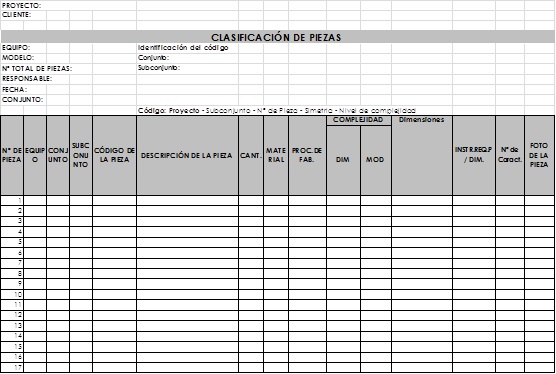
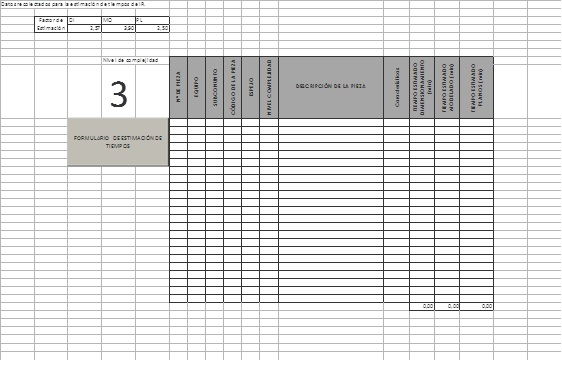
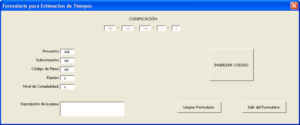
ANEXO # 3. . Clasificación de complejidad de las partes a ser modeladas.
Consta de cinco (5) niveles:
1.- Estándar 2.- Básico 3.- Regular 4.- Compleja 5.- Muy Compleja.
- Estándar: Piezas y/o partes diseñadas y fabricadas bajo estándares conocidos (normalizadas): DIN, ISO, ASTM. Como, por ejemplo: Tornillos, tuercas, remaches, rodamientos, cojinetes, arandelas, o-ring, graseras, retenes, cupillas, chavetas, pasadores sólidos, pasadores de presión, pasador de aletas (cupilla), etc.
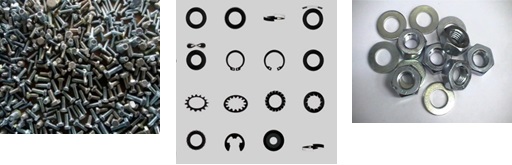
- Básico: Formas geométricas sencillas, determinadas por instrumentos de medidas convencionales, como, por ejemplo: cinta métrica, calibradores, plantillas de radio. Presentan simetría con respecto a todos los planos de referencia.
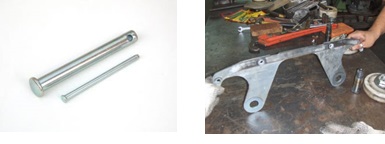
- Regular: La forma externa puede ser asimétrica en uno (1) de los planos de referencia. Su forma externa puede ser caracterizada por medio de instrumentos convencionales como calibradores (digitales o analógicos), cinta métrica, gramil de altura, tornillo micrométrico, plantillas de radios, plantillas de círculos, cuenta hilos. Pueden presentar formas características como agujeros pasantes y ciegos, lisos ó roscados, ranuras pasantes, chaflanes, biseles, chaveteros, descargas de rectificado, arreglos que pueden ser caracterizados por calibrador.
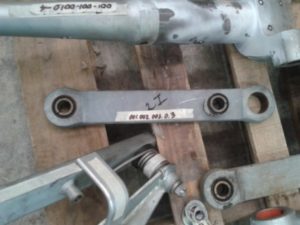
- Compleja: La forma externa puede presentar asimetría hasta en dos (2) de los planos de referencia principales. Si su forma presenta barridos de la sección con evoluciones en la forma (LOFT) o barrido de un perfil simple constante (SWEPT), se deben efectuar en ejes de referencia o contornos que pertenezcan a un mismo plano. Puede presentar características convencionales (ranuras, perforaciones, etc.) adicionales que requieran dimensionamiento convencional. Se contempla el uso de escaneo digital. Puede requerir toma de datos mixto (convencional – escaneo digital). También pertenecen a esta categoría las partes que presentan curvaturas en superficies y/o contornos de radios mayores a los medibles en las plantillas convencionales de radios o curvas, aun siendo simétrica en todos los planos principales.
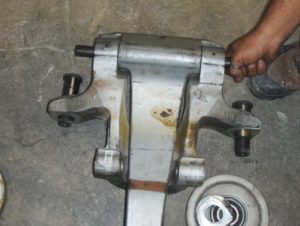
- Muy Compleja: La forma externa presenta asimetría en tres (3) de los planos de referencia principales. Si su forma presenta barridos de la sección con evoluciones en la forma (LOFT) o barrido de un perfil simple constante (SWEPT), se deben efectuar en ejes de referencia o contornos que pertenezcan a dos (2) o más planos. Se contempla el uso exclusivo de escaneo digital aunque también pueden presentar características convencionales (ranuras, perforaciones, etc.) adicionales, que requieren dimensionamiento convencional. Puede requerir toma de datos mixto avanzado (escaneo digital – CMM).
Características específicas de las partes. El número de características específicas de cada parte son aquellas dimensiones generales que son necesarias para describir la pieza a ser modelada junto al conteo de características adicionales que presenta la parte tales como número de perforaciones, radios, chaflanes, perforaciones roscadas, formas específicas en cada uno de los planos principales, etc.
ANEXO #4. Sistema de Codificación.
Los caracteres del código son numéricos y la estructura es la siguiente:
XXX . YYY . ZZZ . O . C
XXX: Indica el código asignado al proyecto.
YYY: Indica el subconjunto al que pertenece la pieza o parte.
ZZZ: Indica el código de la pieza.
O: Indica si la pieza posee o no parte espejo o simétrica. Si este carácter es cero (0), no posee. Si es 1, indica que la parte es izquierda y si es 2, la parte es derecha. Si el código es diferente de cero, el modelista sabe que existe una pieza simétrica a la identificada la cual se genera aplicando simetría con respecto a alguno de los planos principales de referencia.
C: Indica el nivel de complejidad de la parte o pieza.
- Estándar.
- Básica.
- Regular.
- Compleja.
- Muy compleja.
REFERENCIAS:
[1] El Fakih, Kaled Chafic / Padilla, José. Fundación Instituto de Ingeniería – Centro de Ingeniería Mecánica y Diseño Industrial. 2014. PROCEDIMIENTO PARA LA ESTIMACIÓN DEL TIEMPO DE MODELADO EN LOS SERVICIOS DE INGENIERIA DE REVERSA.
[2] http://www.brainkart.com/article/Parts-Classification-and-Coding_6418/
Contacto: orlandoaco2@gmail.com