Instrumentación virtual para el control y medición de variables eléctricas de un motor de inducción
Autores: Tomas Ramos, Miguel Arellano, Hermes Rondón / Centro de Ingeniería Eléctrica y Sistemas (CIES). FIIIDT
La Fundación Instituto de Ingeniería para la Investigación y Desarrollo Tecnológico (FIIIDT) diseñó y ejecutó un proyecto enfocado en una planta de saneamiento de agua de ríos con capacidad de producción de 3.000 L/D/100Hab., donde uno de los componentes del sistema consistió de un tanque para Coagulación – Floculación – Sedimentación cilíndrico de 1m³ de capacidad con un motor acoplado a un eje vertical con un mecanismo de agitación y el cual es operado a dos velocidades específicas mientras se le añaden aditivos al agua contenida en el tanque. El principio de operación de esta planta de tratamiento consiste en eliminar todas las partículas en suspensión en el agua que la hacen no aptas para el consumo humano.
En base a esta experiencia, la FIIIDT planteó replicar este diseño a una escala mayor y ampliar el alcance del proyecto a poblaciones con mayor número de habitantes.
Figura 1. Planta de tratamiento de agua de río para 24.000 L/D/300 Hab. [1]
Una de las adaptaciones del diseño propuesto consistió en el cambio del tanque (Coagulación – Floculación – Sedimentación) por uno de mayor capacidad (4m³) de forma cúbica.

El nuevo mecanismo de agitación utilizado en el tanque cubico conformado por dos paletas cuyos ejes dispuestos en paralelo y de forma axial al eje del motor, genera mayor turbulencia durante el proceso de Coagulación – Floculación, transfiriendo estas perturbaciones al acople del mecanismo de agitación con el motor. En todos estos sistemas, los motores se controlan por medio de variadores de frecuencia. En ellos se pueden observar las variables eléctricas y de operación del motor, pero debido a las perturbaciones durante el proceso de agitación, no es posible realizar mediciones correctamente desde la pantalla del panel frontal del convertidor, puesto que los valores mostrados oscilan producto de estas perturbaciones mecánicas que se transfieren a las variables eléctricas.
Por lo anteriormente expuesto, se desarrolló un sistema para medición y registro de variables eléctricas asociadas al motor trifásico, cálculo de la carga en el eje mecánico, y determinar las posiciones angulares definitivas de ambas paletas con la finalidad de minimizar dichas perturbaciones mecánicas.
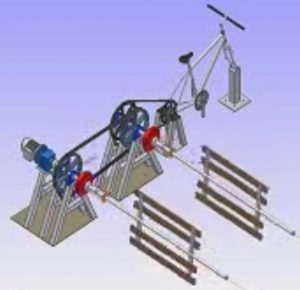
Motor de Inducción 3~208V/60Hz 3HP – Caja reductora 14:1. Fuente [2]
El motor de inducción se encuentra acoplado a una caja reductora de relación 14:1 y el mecanismo de agitación consta de unas paletas dispuestas en dos ejes en paralelo al eje del motor. El tanque de Coagulación-Floculación tiene capacidad de 4 m3 de agua a tratar. Adicionalmente se incorporó una bicicleta adaptada al mecanismo de agitación para alternar en caso de falla del suministro de energía eléctrica a través del sistema fotovoltaico. Este mecanismo de agitación durante el proceso de Coagulación-Floculación debe girar a dos velocidades 60 rpm/15min (velocidad rápida) y 15 rpm/1min (velocidad lenta).
La interfaz virtual desarrollada en el Centro de Ingeniería Eléctrica y Sistemas (CIES) para el control de este sistema se realizó utilizando el entorno de desarrollo LabVIEW. El programa implementado calcula y permite la visualización de las siguientes variables eléctricas en la entrada del motor de inducción: tensiones y corrientes con sus respectivos valores eficaces, valores instantáneos, diagramas fasoriales, frecuencia y potencias (aparente, activa y reactiva), factor de potencia, velocidad y posición angular del mecanismo de agitación; de igual manera, es capaz de controlar la velocidad así como el encendido y apagado del motor.
El Hardware de adquisición de datos (DAQ) de las variables eléctricas de operación está conformada por varias etapas. La etapa “a” consiste en la adquisición de las señales (Sensores + Acondicionamiento de Señales) y la etapa “b” en el convertidor Analógico-Digital (Bornera de Conexión SCB-68 + NI PCI-6229) y la etapa “c” es El Interfaz Hombre-Máquina (conocido por la sigla HMI, del inglés Human-Machine-Interface) para la PC de adquisición, registro, procesamiento y control.
En el acondicionamiento de las señales medidas, se diseñaron en la FIIDT dos tarjetas electrónicas que constan de tres bloques funcionales (Filtro RC Pasabajos, Amplificador de Instrumentación AD620 y Amplificador Aislador AD210), con cuatro canales de acondicionamiento. La primera tarjeta electrónica se encarga de acondicionar las señales de tensión (Entrada: 0-600V/ Salida: 0-10V) y la segunda para acondicionar las señales de corriente (Entrada: 0-60 mV / Salida: 0-10V), específicamente para resistencias shunt, utilizadas para medición indirecta de corriente.
En la etapa del Convertidor Analógico-Digital se utilizó una Bornera de conexiones (SCB-68) y una tarjeta NI PCI-6229. El Bloque conector es de E/S blindado para usarse con dispositivos DAQ de 68 pines de la Serie X, M, E, B, S y R. La tarjeta NI PCI-6229 es una DAQ de la Serie M de 16-Bit Resolución ADC, 250 kS/s, 32 Entradas Analógicas (AI) ó 16 Entradas Analógicas (AI – Diferencial), 48 Entradas/Salidas Digitales (DIO), 4 Salidas Analógicas (AO) +/- 10V (Resolución 16 bits) y Bus PCI, PXI y USB [4]. En la figura 6 se muestra la conexión de todos los componentes del sistema. Además de los mencionados anteriormente, se implementó un protoboard donde se encuentran una serie de borneras con todas las señales de interés juntas (tensiones de línea de las tres fases, tensiones de shunt de las tres fases, bus DC del variador, entre otras).
Variador de Frecuencia: Marca SIEMENS / Modelo Micromaster 440. Fuente [2]
Durante la fase experimental (Figura 7), el sistema prototipo fue probado con y sin carga, realizando las mediciones desde el display del variador de frecuencia.
Las perturbaciones generadas en el acople entre la salida de la caja reductora y el mecanismo de agitación, ocasionaron variaciones importantes en la lectura de los parámetros eléctricos visualizados en el display del variador de frecuencia, dificultando la lectura precisa de las variables eléctricas asociadas a la entrada del motor de inducción. Luego de realizar varios ensayos bajo carga, se obtuvieron por regresión cuadrática el par de carga estimado comparado con el par nominal del motor de inducción y la velocidad angular del eje del motor (Figura 8).
En los datos obtenidos se puede apreciar la estimación de par entregado a las paletas mezcladoras bajo distintas velocidades de operación. Se muestra la curva de carga obtenida con la regresión lineal y los intervalos. El comportamiento es del tipo cuadrático y alrededor de la velocidad nominal, el par producido es de alrededor de 4 N m. El par nominal de la máquina de inducción, calculado con los datos de la placa de la máquina es de 12,32 N m.
La comparación de los datos vistos a través del sistema de instrumentación virtual LabVIEW y medidos a través del sistema de adquisición con aquellos visualizados directamente en el variador de frecuencia se presentan en la tabla 1. Para esta prueba, se registraron los valores con el variador de frecuencia operando en intervalos de 5 hz, iniciando desde 0 hz hasta su frecuencia nominal de 60 hz.
En el siguiente gráfico se muestran los datos de referencia leídos directamente desde el variador de frecuencia comparados con los datos medidos desde el sistema de instrumentación virtual en LabVIEW. Al comparar los resultados entre las dos lecturas, se obtiene que para valores de voltaje el error máximo es del 6% y para la corriente es solo del 2%, por otro lado, para el caso de la potencia y el factor de potencia, el error ya es mayor, con un máximo de 40% para el factor de potencia y un 25% para la potencia activa.
En bajas frecuencias, las señales de referencia (Variador de Frecuencia) y las aproximadas (sistema de interfaz virtual en LabVIEW) son muy parecidas, mientras que al aumentar la frecuencia, se puede apreciar un margen mayor entre ambas señales, relacionado con las frecuencias de conmutación de los transistores bipolar de puerta aislada (conocido por la sigla IGBT, del inglés Insulated Gate Bipolar Transistor) y la estrategia de control del variador de frecuencia. También es importante mencionar que las señales adquiridas por el sistema de instrumentación virtual en LabVIEW son las componentes fundamentales producto del filtro RC (pasa-bajos) conectado en la etapa de acondicionamiento de señales, mientras que las medidas por el variador de frecuencia para las tensiones, son calculadas para la fundamental y todas las componentes de los armónicos.
Una mejor representación de lo indicado anteriormente, es a través de la siguiente, referente al error relativo porcentual, siendo el “valor referencial” los datos obtenidos del variador de frecuencia y el “valor aproximado” los valores medidos con el sistema de instrumentación virtual en LabVIEW. Con esta metodología se cuantifican los errores de la medición mostrados en la tabla 2, para las frecuencias de operación indicadas anteriormente las mediciones indirectas de tensiones y corrientes.
El comportamiento de los errores relativos porcentuales presentados en la tabla anterior de las variables eléctricas medidas (tensiones y corrientes), en distintos puntos de operación. Se puede apreciar que los errores relativos porcentuales se encuentran por debajo del 10% para todas las mediciones realizadas.
Conclusiones
En el hardware (etapa de acondicionamiento de señales) y software (HMI basado en instrumentación virtual usando la plataforma LabView de National Instruments) desarrollado en el Centro de Ingeniería Eléctrica y Sistemas, se logró la adquisición, registro y procesamiento de señales eléctricas, además del control de un motor de inducción por medio de un variador de frecuencia.
Durante la fase experimental del mecanismo de agitación del tanque para Coagulación – Floculación – Sedimentación y producto de la geometría de dicho tanque como la disposición de las paletas, la turbulencia del agua generó perturbaciones mecánicas – eléctricas importantes.
Las variables eléctricas asociadas al conjunto Motor-Reductor no eran posibles medirlas desde el panel frontal del convertidor estático de potencia (variador de frecuencia) debido a que presentaban variaciones considerables y las mismas eran mostradas en formato numérico en una pantalla de cristal líquido (LCD, sigla del inglés liquid-crystal display).
Por medio de esta interfaz (HMI) se logró medir de forma indirecta, visualizar y calcular todas las variables eléctricas – mecánicas asociadas al motor de inducción como la posición angular del mecanismo de agitación. Dichos resultados mostrados en distintos formatos gráficos y numéricos.
Referencias
[1] Diseño preliminar de unidades prototipos para una planta de potabilización de agua de río en comunidades indígenas del Delta del Orinoco de hasta 300 habitantes. Fundación Instituto de Ingeniería. 2017.
[2] XIII CIMENICS. Congreso Internacional de Métodos Numéricos en Ingeniería y Ciencias Aplicadas. Fundación Instituto de Ingeniería – Sistema de Instrumentación Virtual para el Control y Medición de Variables Eléctricas de conjunto Motor de Inducción – Reductor. 2016.
[3] Hernández, S., Sistema de Potabilización para comunidades Warao de 250 Habitantes. Fundación Instituto de Ingeniería – Documento de Asesoría, 2013.
Contactos: tomasenriqueramosmesa@gmail.com ; ma.arellanob@gmail.com